Industrial Floor Coating Contractors: Epoxy Solutions for Manufacturing
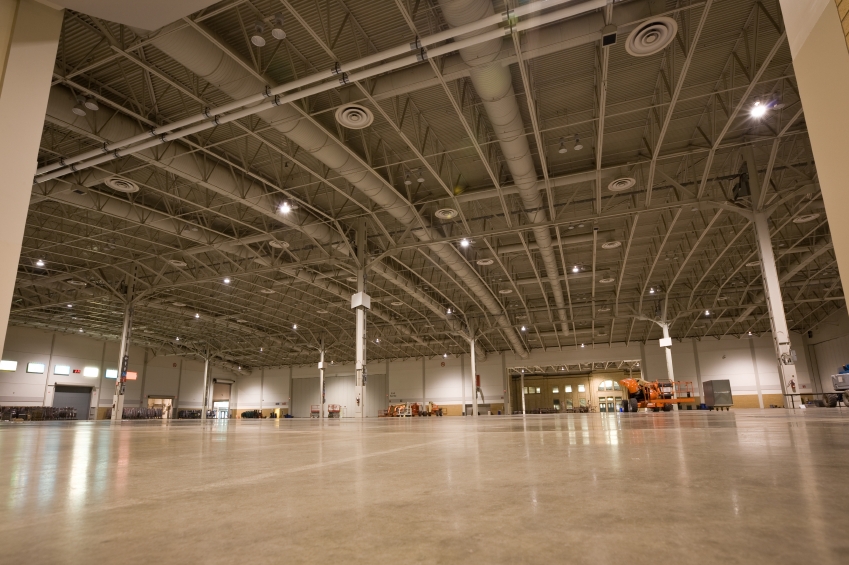
Industrial floor coating contractors are essential for manufacturing facilities seeking durable, long-lasting flooring solutions. Epoxy floor coatings offer exceptional benefits, including improved safety, increased productivity, and reduced maintenance costs. Let’s explore the importance of choosing the right industrial floor coating contractor and the advantages of epoxy coatings for manufacturing environments. We’ll cover topics such as understanding different coating types, evaluating contractors, the installation process, maintenance tips, and how partnering with a reputable contractor can unlock your facility’s full potential. By investing in high-quality epoxy flooring, you can transform your manufacturing space into a safer, more efficient, and visually appealing workplace.
Understanding Industrial Floor Coatings
Epoxy Floor Coatings: A Durable and Versatile Choice
Industrial floor coatings are specialized systems designed to protect and enhance concrete floors in demanding environments such as manufacturing, food processing, and chemical facilities. Epoxy floor coatings offer exceptional durability and can be used in many different types of facilities. They form a tough, chemical-resistant barrier over the concrete.
Epoxy coatings come in various colors and can be textured or non-slip to meet workplace safety standards. The versatility of epoxy also allows the finished floors to withstand heavy impacts and loads in busy manufacturing plants. Cleaning harsh chemicals is easy due to epoxy’s impervious surface. Overall, epoxy flooring systems provide long-lasting protection from wear for concrete floors that undergo constant use in industrial settings.
Manufacturers form epoxy coatings by combining two components: a resin and a hardener. When mixed, these components create a tough, seamless surface that adheres firmly to the concrete.
The coating adheres strongly to concrete surfaces. It creates a protective layer that withstands heavy use. Epoxy protects from chemicals and withstands scratches and bumps. Areas with lots of people or vehicles need durable flooring. The coating endures these high-traffic spots well. It also resists exposure to harsh chemicals that spill or leak. This makes epoxy a good choice for places with demanding conditions. Whether facing wear from footsteps or damage from spilled chemicals, the coating protects concrete from these hazards.
Epoxy flooring provides a durable and long-lasting surface. Its chemical resistance and toughness hold up against heavy traffic and harsh conditions found in many commercial and industrial spaces. The coating forms a seamless, monolithic surface impervious to moisture, oils, chemicals, and impacts. This makes it highly suitable for environments such as warehouses, garages, shops, restaurants, and more. The coating is applied as a liquid and then cured to create a glossy, solid finish. Facility managers appreciate how little maintenance epoxy floors require compared to alternatives like concrete. Stains wipe up easily, and the coating does not deteriorate over time with use. Owners choose from an array of visually appealing colors and patterns to complement their brand or brighten interior areas. Whether cooling a warehouse or dressing a retail store, stylish epoxy floors enhance work areas affordably.
Imagine a busy manufacturing facility where heavy machinery and forklifts constantly move across the floor. An epoxy coating would not only protect the concrete from wear and tear but also provide a slip-resistant surface, reducing the risk of accidents. Epoxy floors are important in food processing plants. Strict hygiene standards must be met. The floors must be easy to clean and stop bacteria from growing. This keeps the environment safe and sanitary. Workers need a clean place without germs to make food. An epoxy floor meets these needs. It protects against dirt and illness that could get into the food. People’s health is a big concern when handling the things we eat. A coating that battles germs helps assure safety for all.
Choosing the Right Epoxy Coating for Your Needs
Not all epoxy coatings are created equal. Different formulations are available to meet specific requirements, such as chemical resistance, temperature resistance, or anti-static properties. Proper selection is important for any project. Contractors can assess unique facility needs and recommend suitable systems. Some important factors include chemical exposures, required durability, and desired aesthetics. It is best to consult experts experienced in commercial applications. They will evaluate intended uses and select an epoxy flooring system tailored for the environment. This ensures long-term protection and performance for years to come.
For instance, in a chemical plant, a specialized epoxy coating designed to withstand harsh acids and solvents would be necessary. Experienced contractors know which coatings work best for different environments. A food processing area needs a coating with enhanced slip resistance and antimicrobial properties to keep workers safe. Contractors can recommend the right product and ensure proper installation. They prepare the surface correctly and apply the epoxy flooring properly. This gives the floor a long life and allows it to serve its purpose well. Installing a flooring incorrectly means it may not protect or last. A contractor’s expertise makes sure the job is done right the first time.
By investing in high-quality epoxy floor coatings, businesses can protect their concrete floors, create safer and more productive workspaces, and enhance the overall appearance of their facilities. Durable and versatile floors can withstand the demands of even the toughest industrial environments when using the right coating system. These floors are installed professionally. A tough coating protects a concrete floor from damage in a workspace. It makes the area safe and easy to keep clean for employees. The coating also improves how the facility looks overall.
Importance of Choosing the Right Industrial Floor Coating Contractors
Many factors must be considered when choosing a floor coating contractor. Experience and expertise help contractors fully understand a facility’s unique needs. Materials matter greatly as well – only high-quality products ensure floors last. An experienced contractor knows which coating withstands heavy traffic or chemical exposure best. Their advice creates floors that support smooth operations for years. Safety is paramount, too. A qualified pro implements any application flawlessly to avoid future problems that might put workers at risk. Negotiating fair pricing also requires expertise. The right contractor saves money in the long run with durable, practical solutions.
Evaluating Industrial Floor Coating Contractors
The contractor should have experience working in industrial settings like factories and warehouses. Talk to previous customers about past projects to understand how well the contractor performed the work. Finding references will help show if they complete jobs on time, on budget, and with high-quality results. Do they have a history of satisfying customers with their coating installations? It is also important to choose a company that will stand behind their work. Look for a warranty on materials and workmanship in case any issues come up after the project is finished. Experience working in similar environments will ensure the contractor understands the unique needs of your facility. Finding certifications proves their expertise and ability to handle industrial floor coating projects professionally.
Specialized Expertise
Manufacturing facilities often have unique flooring requirements due to the presence of heavy traffic, exposure to chemicals, and the need for clean and sanitary surfaces. It was crucial to find a contractor familiar with industrial floor coatings. The contractor needed experience applying epoxy and urethane coatings. These products are made to last in tough conditions like chemical exposure and heavy traffic. A seamless, easy-to-clean surface is important too. The finishes had to stand up to the work done inside manufacturing plants. Any flooring installed must also be safe and sanitary for employees. Specialty coatings can meet all those needs for industrial applications.
The right contractor can properly coat and protect the floors. They will use quality materials suited to your facility’s needs. Investing in a reputable name may cost more initially. However, it prevents costly repairs and expensive downtime later on. You do not want production to stop because the floor is damaged. A good contractor understands the requirements of your business. They ensure the coating withstands heavy usage and spills from equipment or processes. This protects your investment in the building and operations for years to come. Going with experience pays off to keep the facility running smoothly without interruptions.
Factors to Consider When Selecting a Contractor
There are many Industrial Floor Coating Contractors to choose from for your project. You will need a contractor who is experienced with the specific type of floor you have. They should be able to assess its current condition and recommend the best coating materials. Look for a company that provides a warranty for their workmanship. Getting references from previous commercial clients can help you evaluate the quality of their past projects. Speaking to those customers about whether the contractor showed up on time, kept the work area clean and tidy, and addressed any issues will give you confidence in hiring that company for your job. Be sure to get a written estimate with the projected start and completion dates so you understand the timeline and have expectations set properly. Choosing the right industrial floor coating contractor takes some research but will result in a floor that meets your needs and lasts for years.
Experience and Specialization
Whether in food processing, chemical manufacturing, or distribution centers, different industries have unique needs for their floors. Contractors who are experienced, especially with the specific demands of your industry, will comprehend what is required. Flooring must stand up to different conditions, depending on the business. A contractor focused on industrial applications can anticipate what challenges might arise. You want someone acquainted with the particular situations seen in your type of facility. Finding a specialist means the job will benefit from knowledge dealing with your sector’s special demands.
Product Knowledge and Quality
The contractor uses quality coating systems. Epoxy and urethane protect floors well. Other polymer coatings also suit industry needs. Contractors know which materials last through tough conditions.
The latest flooring products and technologies interest an excellent contractor. They stay informed on advances that strengthen surfaces. Some coatings create a barrier against spills or abrasions. A contractor explains options thoroughly for any project’s demands. The best contractor guarantees satisfaction with materials selected for durability.
Installation Process and Preparation
A professional industrial floor coating contractor will follow a thorough installation process, including proper surface preparation, priming, and application techniques. Proper preparation ensures the coating adheres well and lasts. You should ask them about their preparation method to address any concerns. The contractor needs to explain their process fully for a quality application. Questions help both parties understand expectations and get the best results. Concerns are normal, so discuss any to feel confident moving forward.
Safety and Environmental Compliance
Industrial flooring projects often involve working with hazardous materials and adhering to strict safety and environmental regulations. Protecting workers and the environment is paramount for any flooring project. Choose a contractor who is committed to following all required safety procedures. They should have the proper certifications and always put safety first. Ask about their training, protections for staff, and plans to eliminate risks. A reputable company takes precautions seriously to complete the job without issues. Finding one that keeps people and the planet safe leads to work being done correctly.
Industrial floor coating contractors should have experience installing different types of industrial floor coatings. Finding someone familiar with the specific needs of your facility is important. A professional will assess your space and recommend options suitable for the traffic, chemicals, and demands of your operations. Long-wearing coatings protect concrete and contain spills, but choosing one requires understanding your unique environment. Trust comes from verifying that a company stands behind its work with guarantees. References allow for judging their dedication to client satisfaction over time.
Benefits of Epoxy Floor Coatings for Manufacturing Facilities
1) Improved Safety and Compliance
Epoxy floor coatings provide a safer working environment in manufacturing facilities. These coatings offer excellent slip resistance, ensuring employees can move around without the risk of falling, even in areas with high traffic or where chemical spills may occur. Additionally, epoxy floors are highly chemically resistant, protecting the concrete from corrosive substances commonly found in manufacturing settings.
Compliance with industry regulations and standards is crucial in manufacturing. Epoxy floor coatings help facilities meet these requirements, as they are easy to clean and maintain, preventing the buildup of contaminants that could compromise food or beverage production.
Epoxy flooring creates smooth, durable surfaces. These surfaces can be cleaned thoroughly, ensuring no germs or dirt linger. Facilities that produce food and drinks must have sanitary areas. Epoxy creates such areas. It seals out moisture and liquids spilled on the floor. This protects the floor from damage and makes cleaning simple. Spills no longer soak into bare concrete. They can be washed away easily. This allows the facility to maintain high sanitation standards. meeting the needs of customers who demand safety.
2) Enhanced Aesthetics and Branding with Epoxy Floor Coatings
Epoxy floor coatings not only improve safety but also enhance the overall appearance of manufacturing facilities. These coatings come in a wide range of colors and can even incorporate company logos or designs, allowing businesses to reinforce their branding throughout their workspaces.
An attractive and well-maintained epoxy floor can boost employee morale and create a positive impression on visitors, clients, and potential customers.
A clean and polished epoxy floor displays a company’s dedication to excellence. It shows care for both workers and guests alike. An epoxy floor that shines says the business values quality in all areas. This is significant for companies working with food or drink. A pristine floor assists in ensuring products stay safe. It also helps protect the health of employees on the production line. A floor kept in top condition shows that safety is a top concern. Potential buyers may feel more at ease purchasing from an organization with such evident standards.
3) Improved Productivity and Reduced Maintenance Costs
Investing in epoxy floor coatings can lead to increased productivity and lower maintenance costs in manufacturing facilities. Epoxy floors offer durability and withstand wear and tear.
Epoxy flooring provides protection for manufacturing facilities. It resists damage from heavy equipment, chemicals, and other hazards common in industrial settings. Facilities that use epoxy coating on their floors spend less money on repairs over time. The coating does not need to be replaced very often, like other types of flooring that get worn down quickly. Workers can be more efficient when the floor stays in good condition for a long period of time without constant fixing. Maintaining smooth, safe floors cuts down on disruptions to production. Overall, epoxy coating helps save money by lasting for years with minimum fixing or replacement required during that time.
Epoxy floors provide a low-maintenance surface. They are smooth, so dirt and spills do not get trapped in cracks or seams. Cleanup is simple with just soap and water. This means less time spent scrubbing and more time for important work. Employees no longer must deep clean the floors every weekend. Small cleanups can happen daily or as needed. Now they have extra hours to dedicate to tasks that advance the business. Productivity rises when workers are not distracted by extensive cleaning duties. Their energy stays focused on core responsibilities vital to success. The seamless epoxy coating makes maintenance efficient, so all can contribute to the goals of the company.
Manufacturing facilities see many benefits after installing the new floor coatings. Workers feel safer since the floors are no longer slippery. The owners save money because maintaining the epoxy floors took less time and money than the old floors. Everyone appreciates how much nicer the plant looked with the shiny, clean epoxy floors instead of the dirty, worn-out old floors. Compliance with regulations improve too because any spills or leaks on the epoxy floors are easy to clean up. Whether helping the bottom line or helping workers, epoxy flooring proves a good choice for manufacturing plants.
The Installation Process
Surface Preparation: The Key to Successful Industrial Coatings
Proper surface preparation is the foundation of any successful industrial floor coating installation. It involves thoroughly cleaning the concrete surface, repairing any cracks or damages, and ensuring the floor is free from contaminants that could compromise the coating’s adhesion. The floor must be clean for the coating to stick well. Experienced contractors know that preparing the surface is very important. They use special methods like shot blasting or grinding with diamonds. These ready the floor best for the coating to work its best by giving the surface just the right roughness. Coatings last longer and protect floors better when the surface is ready for them through careful preparation by contractors who understand its significance.
Application: Precision and Expertise
Once the surface is prepared, the application process begins. Epoxy and urethane coatings are typically applied in multiple layers, each serving a specific purpose. Whether it’s a broadcast system for enhanced traction or a seamless, chemical-resistant floor coating, skilled contractors meticulously follow the manufacturer’s instructions to ensure proper coverage and thickness. The contractors’ expertise extends beyond just putting it down, as they also think about things like how warm or wet it is, and if air is moving around. They want the perfect place for it to harden. Their work is careful to make sure it goes on right, so it will be tough. But making it strong is only part of their job – they must create the best conditions for the coating to cure.
Curing: The Final Stage in Industrial Floor Coating Installation
After the coating has been applied, it must be allowed to cure properly. This process can take anywhere from a few hours to several days, depending on the specific product and environmental conditions. The floor is off-limits during the curing time to allow the coating to set and harden correctly. Ensuring it achieves the desired protective properties. Once fully cured and hardened, the industrial floor coating is then ready for use in manufacturing environments. Withstanding heavy usage and providing a durable, easy-to-clean surface. Which enhances safety and improves productivity within the facility.
Minimizing Downtime at Manufacturing Facilities
For manufacturing facilities, minimizing downtime during the installation process is a top priority. Strategic planning helps reduce disruptions to operations. Contractors work with their clients to develop a careful schedule. They consider scheduled shutdown periods. Or coating some areas while others continue running. This lets the facility function in parts. While other sections receive new flooring. Coordinating carefully keeps disturbances low for important work.
The contractors have the expertise to transform the manufacturing space quickly. They can apply a high-performance industrial floor coating to update the facility. Doing so respects the client’s production needs and allows minimal interruption. With efficient techniques, the space can be updated over the weekend or just in the in the evenings. The contractors leverage their experience to work within the operational schedules. The facility then is back open with a new floor that meets requirements but has caused little lost time. The professionals get the job done on time while not disrupting regular business too much.
Maintenance and Longevity
Regular Cleaning and Inspection
The factory floor needed regular maintenance to keep it safe. They checked the floor coating every month for signs of wear. Small cracks or bubbles in the epoxy could be repaired before causing bigger problems. Last year, a section started to peel up near the loading docks. The crew fixed this right away by grinding away the loose bits and applying fresh coats of the tough formula. It protected the concrete below from spills and wear over the long haul. Without the durable coating, the floor wouldn’t last nearly as long under the heavy machines. They were glad it was still going strong after five years of steady use. Proactive upkeep kept it performing well for manufacturing.
The floor required cleaning every day to remove dirt and debris. Thorough cleanings addressed spills in high-traffic zones. We considered a schedule using products the maker suggested. Some cleaning involved special tools. For busy areas, we aimed to clean more deeply. The schedule helped keep the floor looking its best. Manufacturers provide guidance for a reason. Following directions helped the coating last. Some tools made the work faster too. Whether by hand or machine, the cleaning mattered. It protected the epoxy from wear over time.
Periodic inspections are equally important to identify any signs of wear, cracks, or damage to the epoxy coating. Early detection of these issues can prevent further deterioration and costly repairs down the line. Pay close attention to areas during inspections. Heavy foot traffic, chemical spills, or impact from machinery and equipment can damage these areas. Look for signs of wear in locations that see a lot of use. Spills and collisions with equipment may cause cracks or chips in the protective coating. Inspect regions that face these stresses carefully for any flaws. Early finding of problems allows time to fix issues before they worsen, saving money in the long run.
Proper Maintenance Techniques
To ensure the longevity of your epoxy floor coatings, it’s essential to follow the proper maintenance techniques. Proper maintenance involves routinely reapplying a clear topcoat or sealer to protect the surface. It also enhances the flooring’s durability over time. Additionally, promptly addressing any cracks or chips can prevent further damage. Patching or resurfacing affected areas extends the life of the coating. Cleaning up spills right away keeps the floor looking its best for longer. Regular sweeping and occasional washing removes dirt and debris that could dull the shine or allow moisture to seep into tiny openings. Minor damage addressed soon won’t become major problems down the road. With low-effort upkeep, an epoxy floor coating can serve well for years to come.
Consulting with experienced industrial flooring contractors can provide valuable insights into the best maintenance practices for your specific manufacturing facility. Proper upkeep keeps your epoxy floors looking their best. Contractors understand what cleaning supplies and schedules work well for different factory environments. They see what does and does not last over time. Talking to professionals helps pick routines that protect your investment. Cleaning too much or too little could hurt the coatings quicker. Contractors will guide you towards the amount that maximizes how long the floors perform well for your space.
Epoxy flooring provides durability and longevity when installed correctly and maintained properly. A well-designed maintenance program allows the floors to withstand the demands of manufacturing while keeping the workspace safe, productive, and attractive. Short inspections find small problems before they become large issues. Regular cleaning removes dirt and debris that can damage the coating over time if left alone. Following the maintenance schedule preserves the floor’s appearance and protects the investment in the durable epoxy surface. Proper techniques, like those in the plan, are important to maintain the floors as manufacturing needs change. With care, the floors can serve your facility’s operations for many years to come.
Partnering with the Right Industrial Floor Coating Contractor
The Importance of Choosing the Right Contractor
The contractor you choose must know how to properly install the coating. Epoxy floors and coating systems require skill to apply correctly. If not done right, they may not hold up to the traffic and conditions in your facility. Look for a company that will suggest options tailored to your needs. Whether you need a surface that withstands high use in manufacturing. Or a coating made for resistance against chemicals in food production. An experienced contractor understands the different demands. They can recommend the coating best suited to the environment in your plant. This ensures your investment protects the floor as intended for years to come.
Doing Your Research and Asking for References
Before making a decision, it’s essential to do your research and ask for references. Look for contractors with a proven track record in the industry, and read testimonials from their previous clients. The contractor should give you pictures of projects before and after they worked. They need to tell you about the things and methods they use. A good contractor will show you what work they have done in the past. They must be ready to share portraits of work not yet done along with work now finished. Also, reliable details ought to be provided regarding the items and techniques applied.
Long-Term Benefits of Investing in Quality
Quality materials and workmanship are important for any commercial flooring project. Cheaper options may seem like a better value initially but often don’t last as long. Over time, a floor with a low-quality coating will need to be repaired or replaced more frequently than one done correctly from the start. This means recurring costs that outweigh the savings from the lower initial price. Opting for an experienced installer and durable epoxy coating chosen for your specific site needs will better serve the long-term interests of any business or organization. Though there is an upfront investment, avoiding premature wear saves money in the long run. Plus, satisfied customers and workers in a location with an attractive, functional floor can benefit a company in other valuable ways too.
Epoxy floors offer more than functionality alone. Their beauty comes from many options in color and texture. You can craft a design that matches your company’s image. It brings visual cohesion and enhances the look of work areas. Different shades allow customization to highlight zones. A smooth finish provides an appealing backdrop. Textured surfaces add pop and prevent slips. The variety ensures something for every taste and task. Properly applied, they beautify workspaces with low maintenance charm.
Elevating Your Manufacturing Facility with Epoxy Floor Coatings
Epoxy floor coatings can transform your workspace. They create a durable, low-maintenance, and visually appealing environment for your manufacturing facility. Contact us today to unlock this potential for your operations. An epoxy floor protects against damage from equipment, chemicals, and weathering. It provides a clean, safe workspace where spills and debris no longer pose a slip hazard. Your employees will appreciate the improved conditions. A colorful epoxy floor also boosts morale in the workplace. Custom designs and logos allow you to showcase your company’s brand throughout the facility. Protecting your facility’s floor now prevents costly damage later. Boston Concrete Floor Coatings can install an epoxy floor coating tailored for your facility’s needs. Reach out at (203) 912-7244 to discuss how they may enhance your manufacturing operations through a durable, long-lasting flooring solution. A free quote shows the advantages and value for your budget.